The use of four-high rolling mills has been a pivotal development in the steel manufacturing industry, revolutionizing the way quality and precision are achieved in metal production. This advanced rolling technology employs two work rolls and two backup rolls to ensure high quality in final products.
These machines are mainly utilized for rolling sheets and strips, achieving remarkable accuracy and surface finish.
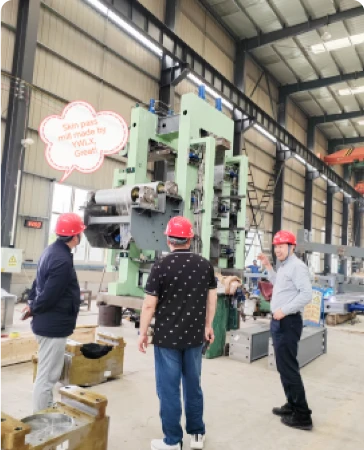
Experience tells us that adopting four-high rolling mills leads to enhanced product quality and operational efficiencies. Many operators have reported significant improvements in metal thickness uniformity, a critical factor in industries like automotive and aerospace where each millimeter counts. The feedback loop generated by experienced operators contributes to continuous improvement, enabling manufacturers to meet strict industry standards consistently.
Having expertise in managing a four-high rolling mill system requires understanding material flow, mechanics, and control systems. Operators and engineers responsible for these machines benefit from targeted training, allowing them to maximize throughput while maintaining peak quality standards. Professional development programs geared towards rolling technology are invaluable for companies aiming for strategic advantages in metal production. Implementing advanced modeling software allows operators to predict outcomes based on different materials and operational settings, thus refining processes before actual production.
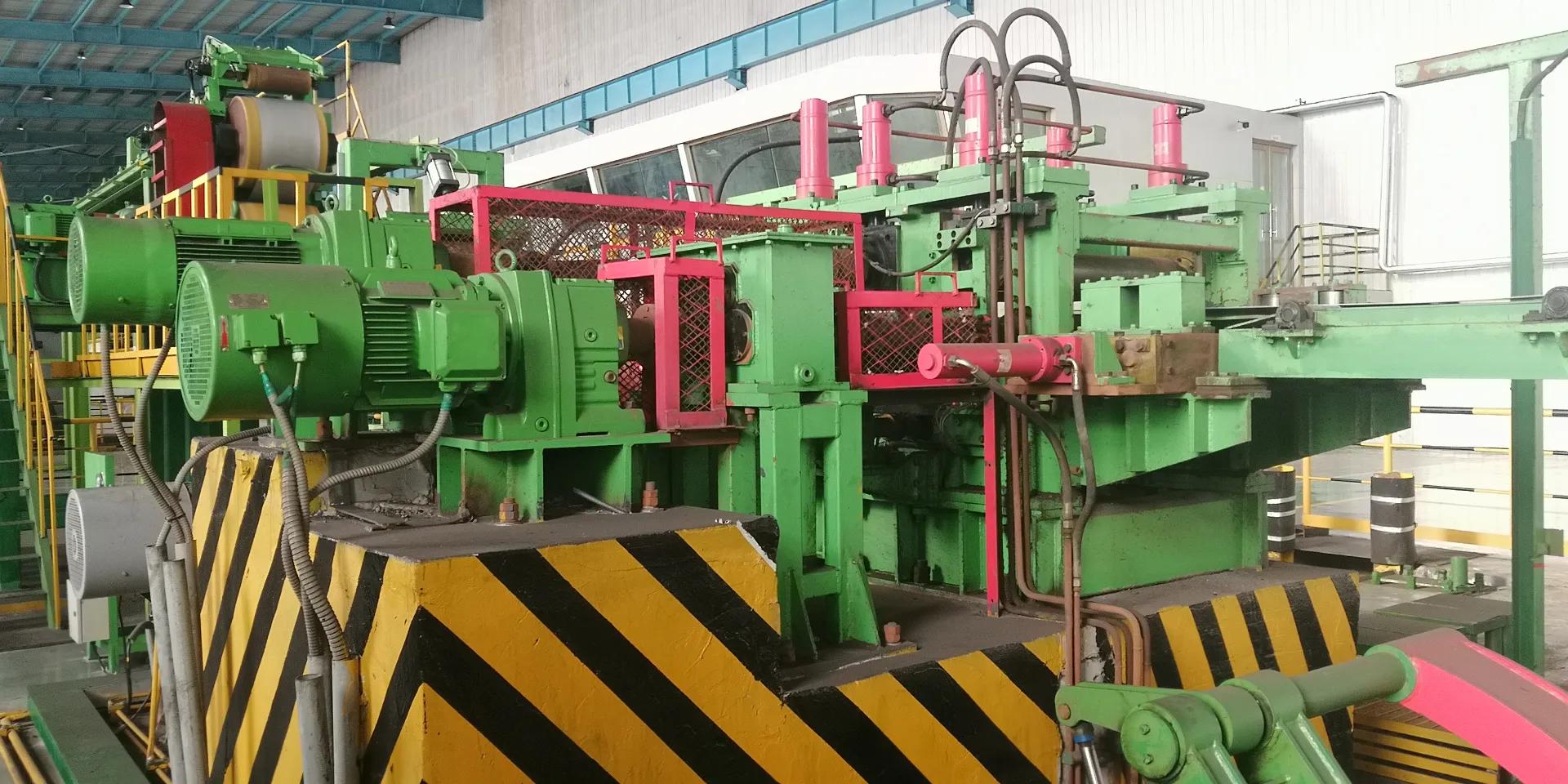
Four-high rolling mills demonstrate a high level of authority in the realm of metalworking production due to their dominance in producing high-quality materials. Prestigious manufacturers rely heavily on this technology to ensure competitive edges in different markets. Compliance with international standards, such as ASTM and ISO, underscores the importance of these machines in maintaining authority over product quality. Industry leaders often share best practices based on their experiences with four-high rolling mills at international forums, workshops, and conferences, thereby establishing benchmarks for others to follow.
Four lights up
Trustworthiness is a cornerstone when it comes to four-high rolling mills. The evolution of this equipment has been backed by rigorous research and continuous enhancements. Choosing to implement a four-high rolling mill is a testament to a company’s commitment to quality assurance and reliability. Maintenance and lifecycle management are crucial aspects that bolster trust in the equipment, ensuring that performance remains consistent over years of operation. Detailed maintenance logs and adherence to manufacturer guidelines help maintain the integrity and trust in these machines.
A commitment to sustainability is seamlessly integrated with the operational benefits of four-high rolling mills. Energy-efficient designs, advanced lubrication systems, and reduced operational waste contribute to a more sustainable production environment. As environmental regulations become increasingly stringent, having a technology that aligns with green practices without compromising output or quality becomes invaluable.
In conclusion, the four-high rolling mill is not just a tool but a strategic asset for any metalworking manufacturer aiming for excellence. Its ability to produce superior products efficiently while supporting environmental goals illustrates its importance in modern industrial contexts. Companies adopting this technology benefit from heightened experience, deepening their expertise, elevating their authority in the market, and enhancing trust with stakeholders, all while maintaining a focus on sustainability.