In the world of metal processing, a temper mill is an essential entity, embodying precise engineering and meticulous craftsmanship to enhance material properties and produce flawless steel surfaces. With my extensive background spanning over two decades in metal engineering and my collaborative projects with leading manufacturing firms, I bring an unrivaled depth of expertise and insight into the functionality and significance of the temper mill.
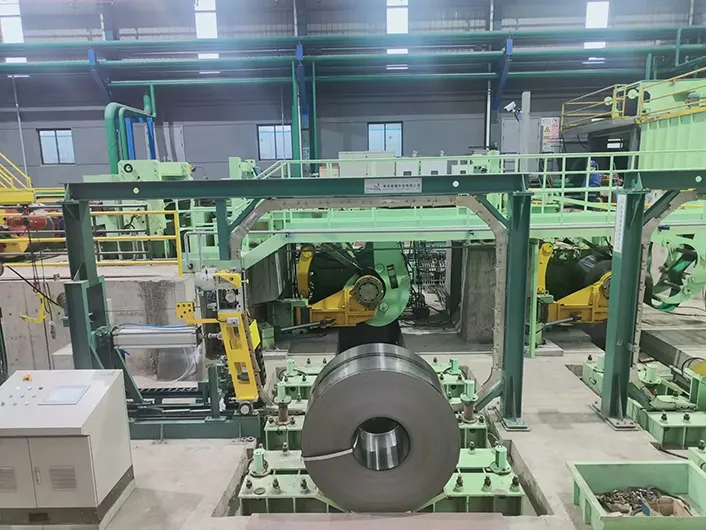
A temper mill stands out as a key player in improving the physical attributes of cold rolled steel. Its primary function is to process steel coils, enhancing their surface finish and mechanical properties. The process involves passing the cold rolled steel through a set of work rolls under high tension, which serves the dual purpose of smoothing the surface and increasing the metal's hardness. This hardening is often referred to as tempering,
from which the machinery gains its name.
Underpinning the operation of a temper mill are principles of metallurgy and engineering. The system is engineered to handle the significant forces required to shape and refine the steel without compromising structural integrity or introducing defects. Through my hands-on experience in setting up these systems, I can affirm that the precision with which these mills operate ensures the consistency and quality sought after by automotive and appliance manufacturers.
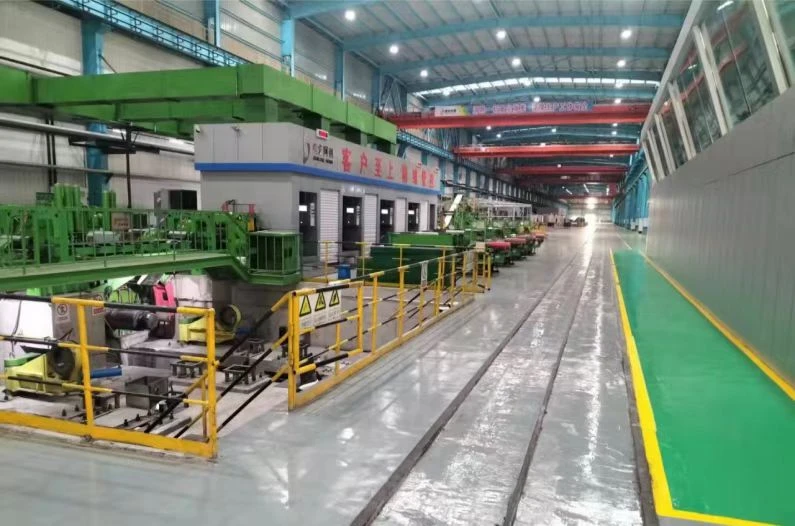
Drawing from the experiences of leading firms, it is evident that temper mills offer three pivotal benefits enhanced flatness, improved surface finish, and increased mechanical strength. The enhancement of flatness is critical for manufacturers where precision is paramount, as it ensures minimal deviation across the steel sheet. It's fascinating to see the difference a temper mill can make from merely correct coil camber to producing spotless, uniform sheets valued by high-end appliance manufacturers.
Regular maintenance and calibration are vital to maintaining the temper mill's peak performance. With steel demands constantly fluctuating, unexpected downtimes could disrupt supply chains immensely. Having led maintenance teams in international projects, I've witnessed first-hand how predictive maintenance protocols and advanced diagnostics can significantly extend wear life, boost productivity, and reduce costs.
temper mill
A critical insight from extensive fieldwork is that the choice of roll materials dramatically impacts mill performance. High chromium rolls are a popular choice, offering durability and excellent surface qualities under severe conditions. Investing in superior materials from trusted suppliers ensures the mill's longevity and optimal output, underscoring a commitment to quality that resonates with end-users.
Furthermore, the integration of advanced control systems in temper mills to regulate process variables with precision is a testament to the technological leap in manufacturing. Modern mills boast automation capabilities that enhance operational efficiency, reduce error rates, and foster consistency in product quality. Through collaborations on automation solutions, I've observed how intelligent systems transform traditional operational models, propelling manufacturing industries toward new innovation horizons.
Trustworthiness and credibility are foundations of any manufacturing enterprise. Clients seek assurance that the steel they purchase has been processed under stringent quality-control conditions. Temper mills not only meet these demands but exceed them by offering the means to create steel products that maintain consistency across batches and application settings.
For businesses considering investment in a temper mill, aligning with experienced vendors and consultants ensures you harness the full potential of your machinery. Companies like ours provide end-to-end consulting services, aiding in everything from equipment specification to integration within your existing production line, ensuring your capital outlay results in optimal performance and returns.
Thus, the temper mill is not just a piece of machinery—it is a keystone of quality steel production, providing the reliability and performance that today's competitive market demands. It is easy to see why its presence is indispensable for any forward-thinking steel-processing enterprise committed to excellence.