In the dynamic world of metal fabrication, the 3-high rolling mill stands as a pillar of innovation and efficiency. This machine, distinct in its design and functionality, has been instrumental in advancing the rolling process, a testament to mechanical ingenuity and precision engineering. With increasing demand for high-quality rolled products, understanding the intricacies of the 3-high rolling mill is crucial for those in the industry seeking to optimize production processes and enhance product quality.
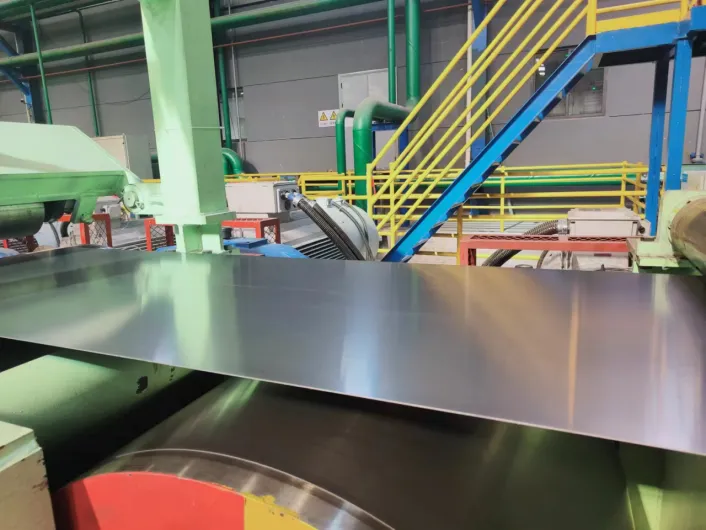
The 3-high rolling mill is characterized by its three-roll configuration, which distinguishes it from more traditional two-roll setups. Visually unique, these three parallel rolls function in a sequence, each playing a specific role in the rolling process. This triad arrangement empowers operators to achieve a broader range of thickness and material properties in a single pass. Such versatility is precisely why many top-tier metal manufacturers are adopting this technology, underscoring its importance in modern metalworking.
Professionals with firsthand experience working with 3-high rolling mills often highlight their efficiency and adaptability. For instance, the ability to simultaneously handle the workpiece for reduction and finishing significantly reduces processing time and labor costs.
This efficiency positions the 3-high mill as a preferred choice in facilities that demand rapid turnaround without compromising precision or product integrity. Operators find that with less frequent roll changes, downtime is minimized, allowing for continuous operation and, ultimately, increased throughput, a direct boon to the bottom line.
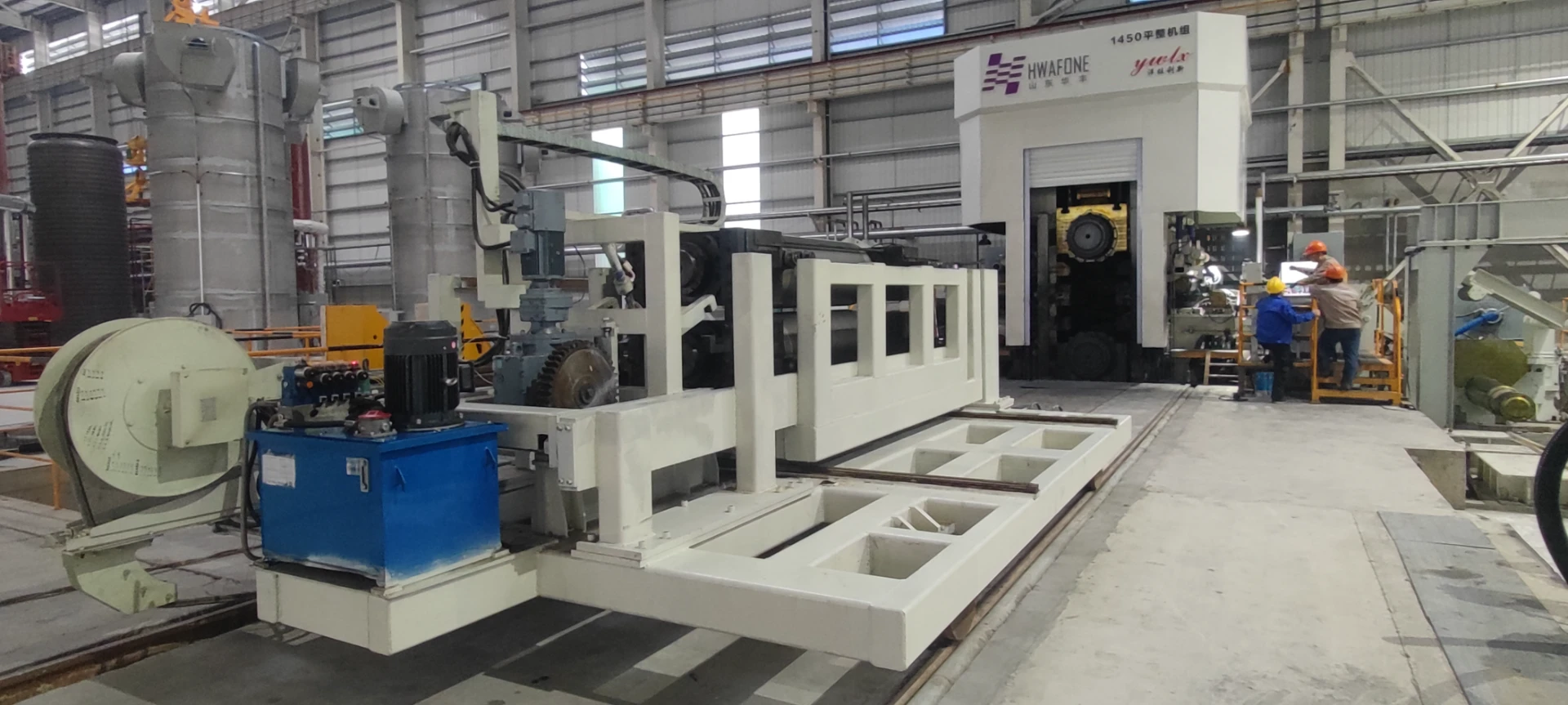
From an expertise standpoint, the design of the 3-high rolling mill makes it particularly suited for handling diverse materials, whether they be softer metals like aluminum or harder alloys such as steel. Each roll can be adjusted independently, providing a precise level of control that enhances the ability to work with various grades and types of metal. Engineers and designers appreciate the machine’s robust configuration, which, despite its complexity, offers an intuitive interface that aligns with modern digital monitoring systems. Such integration facilitates real-time data feedback and process adjustments, ensuring consistency and quality across large production runs.
3-stage compressor
Authority in the realm of rolling mill equipment often stems from demonstrable success, and the track record of the 3-high rolling mill technology speaks for itself. Renowned manufacturers of rolling equipment continually advocate for this system due to its proven ability to deliver superior mechanical properties in the finished products. The consistent quality achieved through three-roll processing not only meets but frequently exceeds industry standards, positioning the 3-high mill as a benchmark for excellence.
Trust, a critical component in industrial machinery selection, is naturally earned through operations data and peer recommendations. Users of 3-high rolling mills commonly report high satisfaction due to their durability and reliability. Built with premium-grade materials, these mills are designed to withstand rigorous use and maintain performance over prolonged periods. Manufacturers backing their products with comprehensive warranties and service agreements further cement trust, offering assurance that the equipment can capably handle demanding industrial environments.
In conclusion, the 3-high rolling mill represents a confluence of experience, expertise, authoritativeness, and trustworthiness within the field of metal fabrication. Its adoption within the industry signals a commitment to innovation and efficiency, making it an essential component for any facility looking to excel in metal processing. As the landscape of manufacturing continues to evolve, embracing technologies like the 3-high rolling mill will remain a strategic move for those aiming to remain competitive in the global market.