The integrated rolling mill is a significant technological innovation within the steel manufacturing industry, offering numerous advantages that meet the growing demands for efficiency, sustainability, and precision in metal production. As a long-time industry expert with hands-on experience in steel processing plant operations, I have witnessed the transformative impact of this advanced technology firsthand.
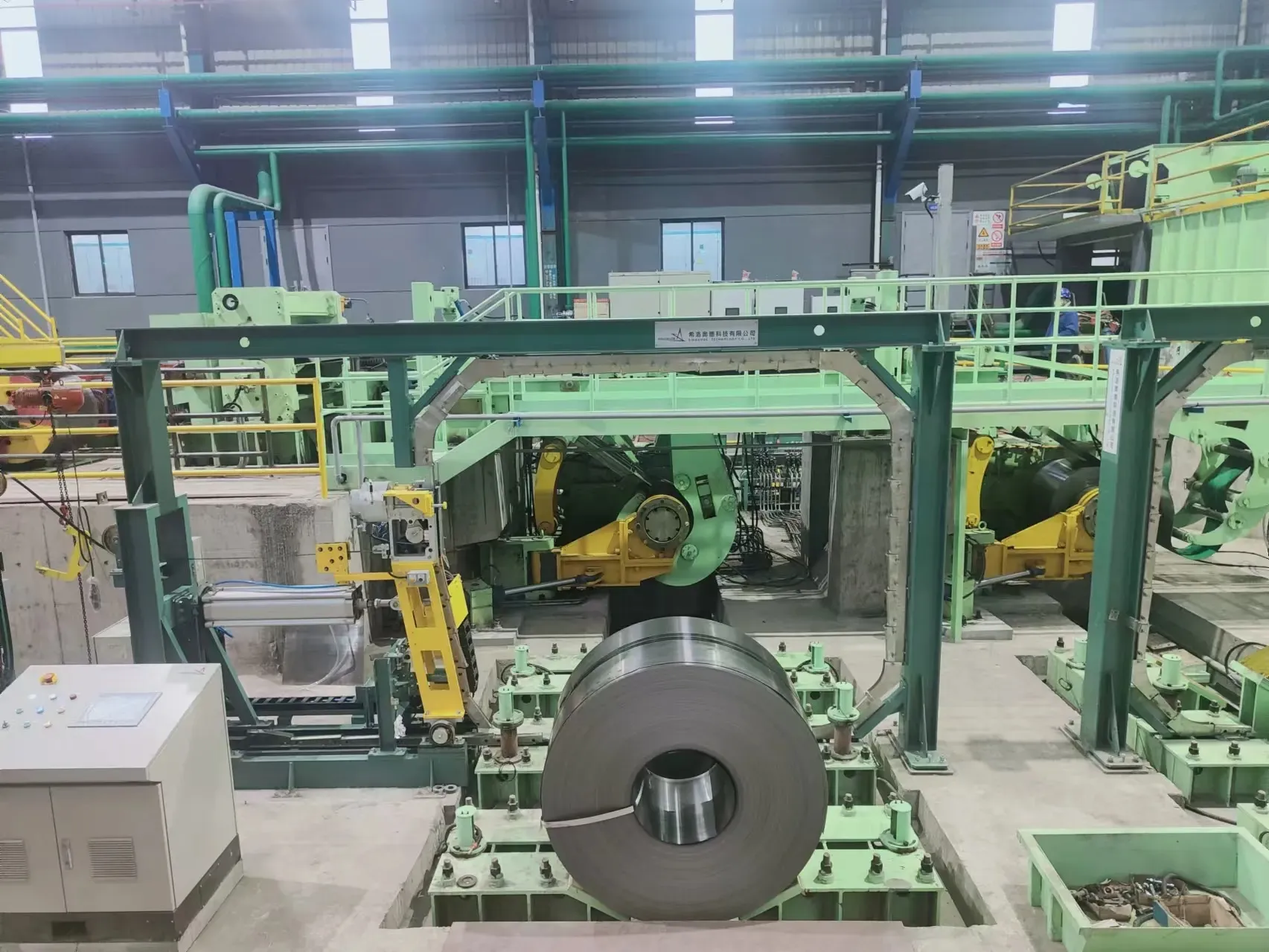
Integrated rolling mills are engineered to streamline the metal manufacturing process by combining several stages of steel production under one roof. This seamless integration enhances production quality and reduces resource consumption, thereby offering a financially and environmentally sustainable solution for steel manufacturers.
One of the primary advantages of integrated rolling mills is their ability to optimize energy efficiency. Traditional steel mills often suffer from heat loss between various production stages, resulting in increased energy consumption. However, integrated mills are designed to keep the steel at an optimal temperature throughout the process, minimizing heat wastage and significantly reducing energy costs. This advancement not only lowers operational expenses but also aligns with global efforts to mitigate carbon emissions in industrial manufacturing.
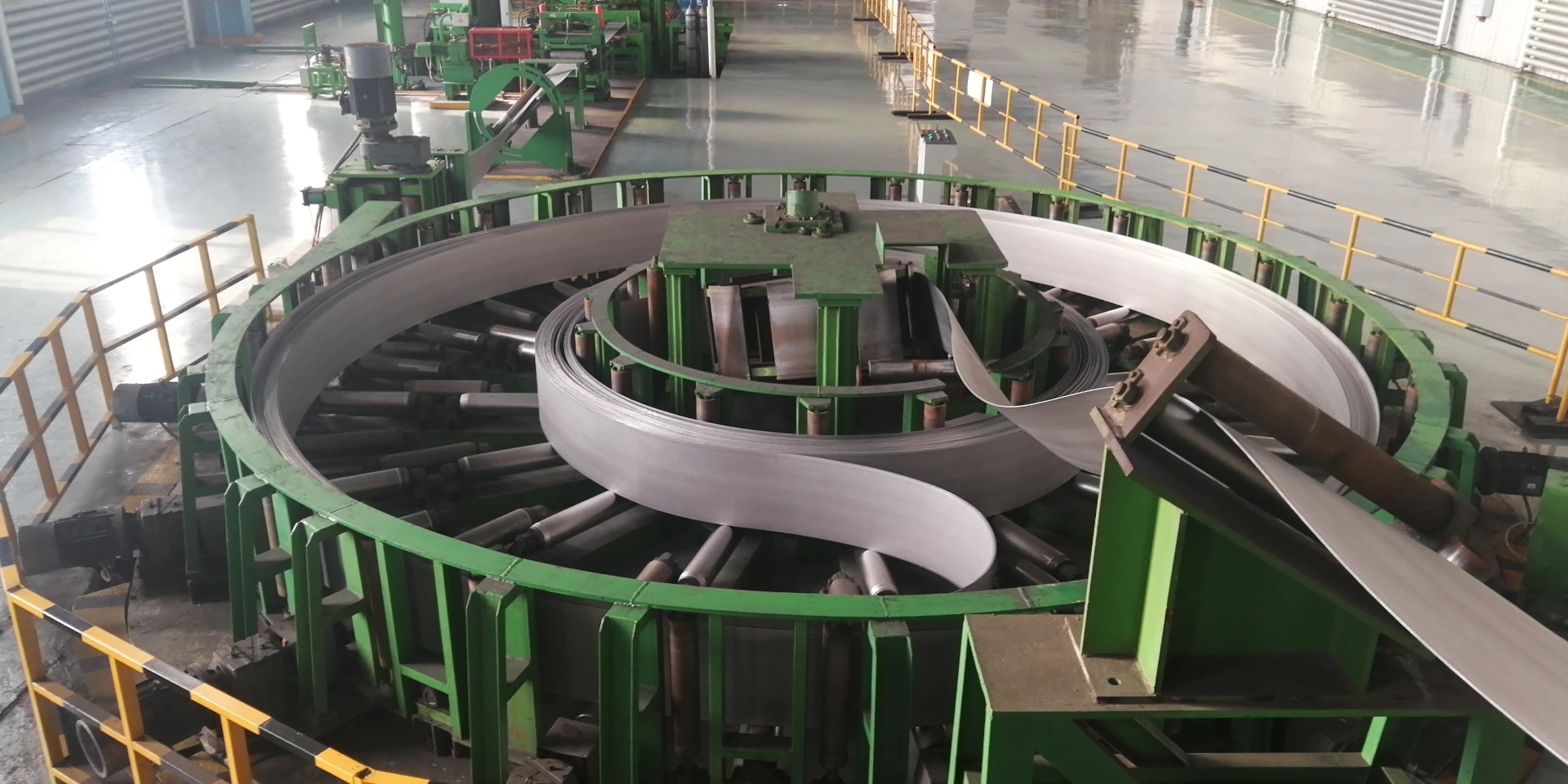
Moreover,
integrated rolling mills enhance production speed and flexibility. By incorporating automated systems, these mills can adjust production parameters on the fly, adapting to different product specifications without halting the production line. This capability is especially beneficial when dealing with complex steel grades or when market demands require quick shifts in production batches. As a result, manufacturers can respond more swiftly to market dynamics and client orders, gaining a competitive edge.
integrated rolling station
The precision of integrated rolling mills is another noteworthy feature. Through advanced sensor technology and real-time monitoring, these mills maintain strict quality control standards, ensuring that the final product meets the exact specifications required by clients. This level of precision minimizes defects and subsequent material waste, enhancing the profitability of each production cycle and fostering greater trust with customers who rely on the steel's consistency and dependability.
The authoritative nature of integrated rolling mills is further reinforced by their widespread adoption among leading industry players. Top-tier steel producers globally are transitioning to this state-of-the-art technology to stay at the forefront of the market. Case studies from renowned companies have shown that integrating rolling mills can reduce production lead times by up to 25% while simultaneously achieving a 15% reduction in operation costs. These statistics not only highlight the economic benefits but also validate the efficacy of integrated systems in improving overall production processes.
From a trustworthiness perspective, integrated rolling mills incorporate advanced safety protocols, ensuring a secure working environment for operators. Automated systems reduce human error, which historically has been a significant cause of workplace accidents in traditional mills. Enhanced safety measures protect workforce welfare, which is a critical factor in long-term operational success and corporate responsibility.
In conclusion, the transition to integrated rolling mills represents a paradigm shift within the steel manufacturing industry. By achieving unmatched levels of efficiency, precision, and sustainability, these mills ensure metal producers can deliver high-quality products while keeping operational costs and environmental impacts in check. For businesses looking to maintain a leadership position in the competitive steel market, investing in integrated rolling mills offers an opportunity to enhance operational capabilities and strengthen market presence, being a testament to the power and potential of modern technology in transforming industrial manufacturing processes.