Skinpass rolls, often referred to in the industry as skinpass-walzen, play a crucial role in the metal finishing process, enhancing surface quality and performance of metal products. This article delves into the intricacies of skinpass rolls, discussing their significance, applications, and the technological advancements that underscore their importance in the metallurgy sector.

Skinpass rolls are specialized tools used in the final processing step of cold rolling operations. They are designed to apply a light reduction of thickness to the rolled metal sheet, which not only improves surface texture but also enhances the sheet's mechanical properties. The primary purpose of skinpass rolling is to achieve a desired surface finish and to improve strip flatness and reduce shape defects, thereby ensuring the material meets stringent manufacturing standards.
The process begins with steel or aluminum coils that have already undergone previous stages of rolling. During skinpass rolling, these coils pass through the rolls with a modest applied force. The effect is a smoothing of the surface finish, elimination of coil breaks, and a subtle work hardening of the material. This step is crucial as it sets the tone for subsequent treatments such as coating or painting, which necessitate an even and defect-free surface.
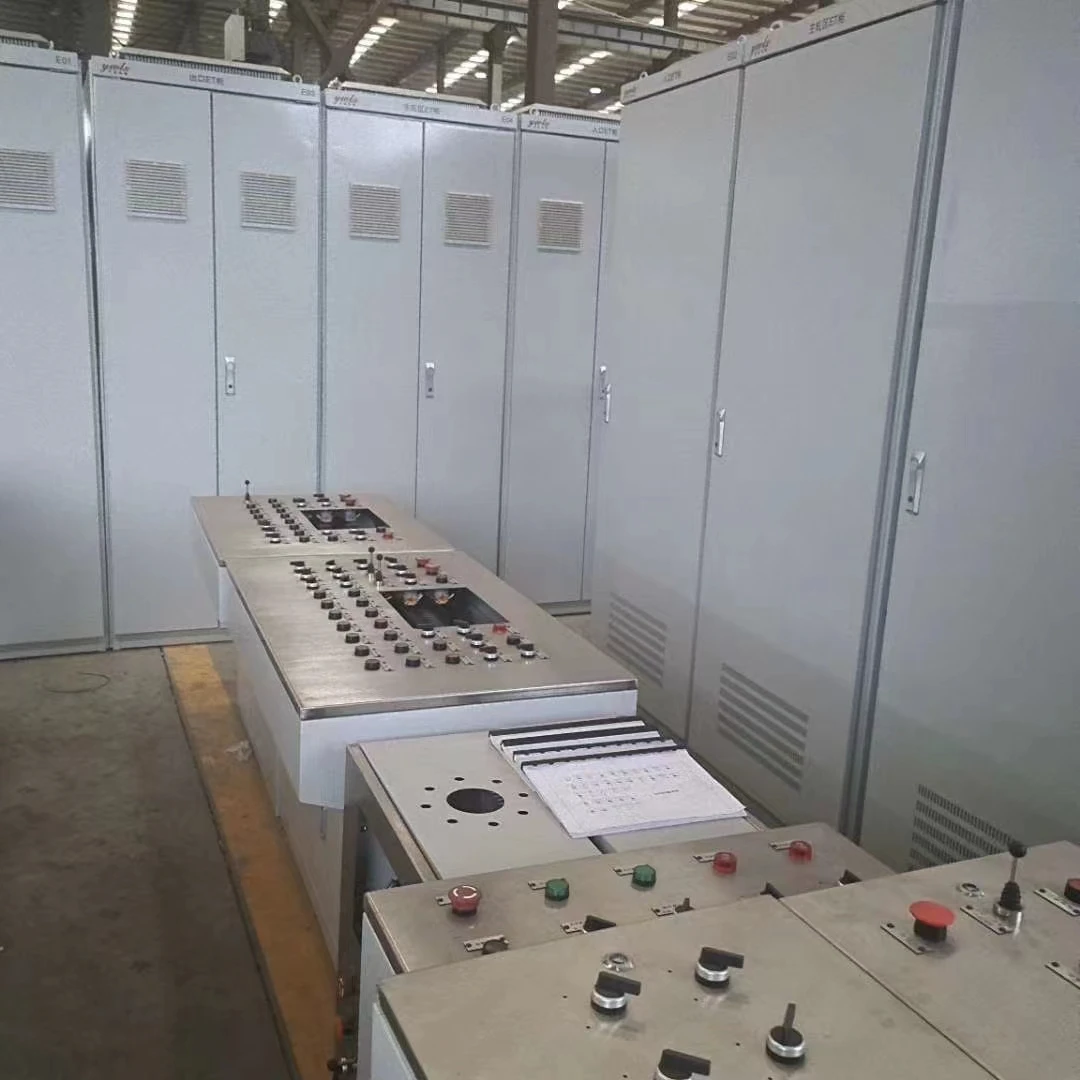
From a modern manufacturing perspective, the role of skinpass-walzen extends beyond traditional applications. Today, these rolls are engineered with sophisticated materials and innovative technologies that enhance their durability and effectiveness. High-performance rolls are constructed using advanced steel alloys and novel metallurgical processes, which provide superior wear resistance and extend the operational life of the rolls. Additionally, the integration of surface coating technologies like chrome plating and tungsten carbide enhances their ability to withstand the rigors of high-speed and high-pressure environments.
A critical aspect of skinpass roll production is precision engineering. The effectiveness of these rolls lies in their precision-ground surfaces, which must meet exacting dimensional tolerances to ensure uniform application of pressure across the width of the strip. Manufacturers utilize state-of-the-art CNC machining and grinding equipment to achieve these specifications, underscoring the expertise and commitment required in roll production.
skinpass-walzen
The demand for skinpass rolls has seen a steady increase with the evolution of high-strength and lightweight materials across various industries. Automotive manufacturers, in particular, have stringent requirements for their sheet metal components, demanding both low weight and high performance. Skinpass rolls play a vital role in meeting these requirements by enhancing the surface quality and mechanical characteristics of automotive steels and aluminums, thereby contributing to vehicle safety and efficiency.
Moreover, in the construction sector, where aesthetic appeal and durability are paramount, skinpass rolls ensure that the metal sheets used in building facades and structures meet both visual and structural standards. The refined surface finish imparted by these rolls allows for flawless applications of coatings and paints, which are essential for protecting metal surfaces from corrosion and environmental degradation.
The prominence of skinpass-walzen in the metal processing industry is a testament to their critical function and the continuing advancements in roll technology. Manufacturers and suppliers of these rolls invest heavily in research and development to improve performance parameters, focusing on enhancing roll life, reducing downtime, and increasing throughput efficiency. By leveraging cutting-edge technology and metallurgical expertise, they ensure that skinpass rolls remain at the forefront of metal finishing solutions.
As the industry progresses, there is a growing emphasis on sustainability and efficiency in metal processing. Skinpass roll technology aligns with these goals by facilitating processes that reduce scrap rates, minimize waste, and improve product yield. Additionally, the development of environmentally friendly coatings and treatments for rolls continues to be a significant focus area for industry leaders, reflecting the broader trends of resource conservation and ecological responsibility.
In conclusion, the expertise embedded in the design and manufacturing of skinpass-walzen showcases the dedication to quality and innovation within the metal processing industry. Their application is indispensable in producing high-quality metal products, ensuring that industries can meet contemporary challenges with precision and reliability. As the demand for superior materials increases, skinpass rolls will undoubtedly remain a fundamental component in the pursuit of excellent surface performance and material excellence.