Integrating industrial rolling mills within manufacturing has revolutionized production processes globally. These sophisticated machines, pivotal in the metalworking industry, transform raw metal into various structural forms, ensuring efficiency, precision, and scalability in production.
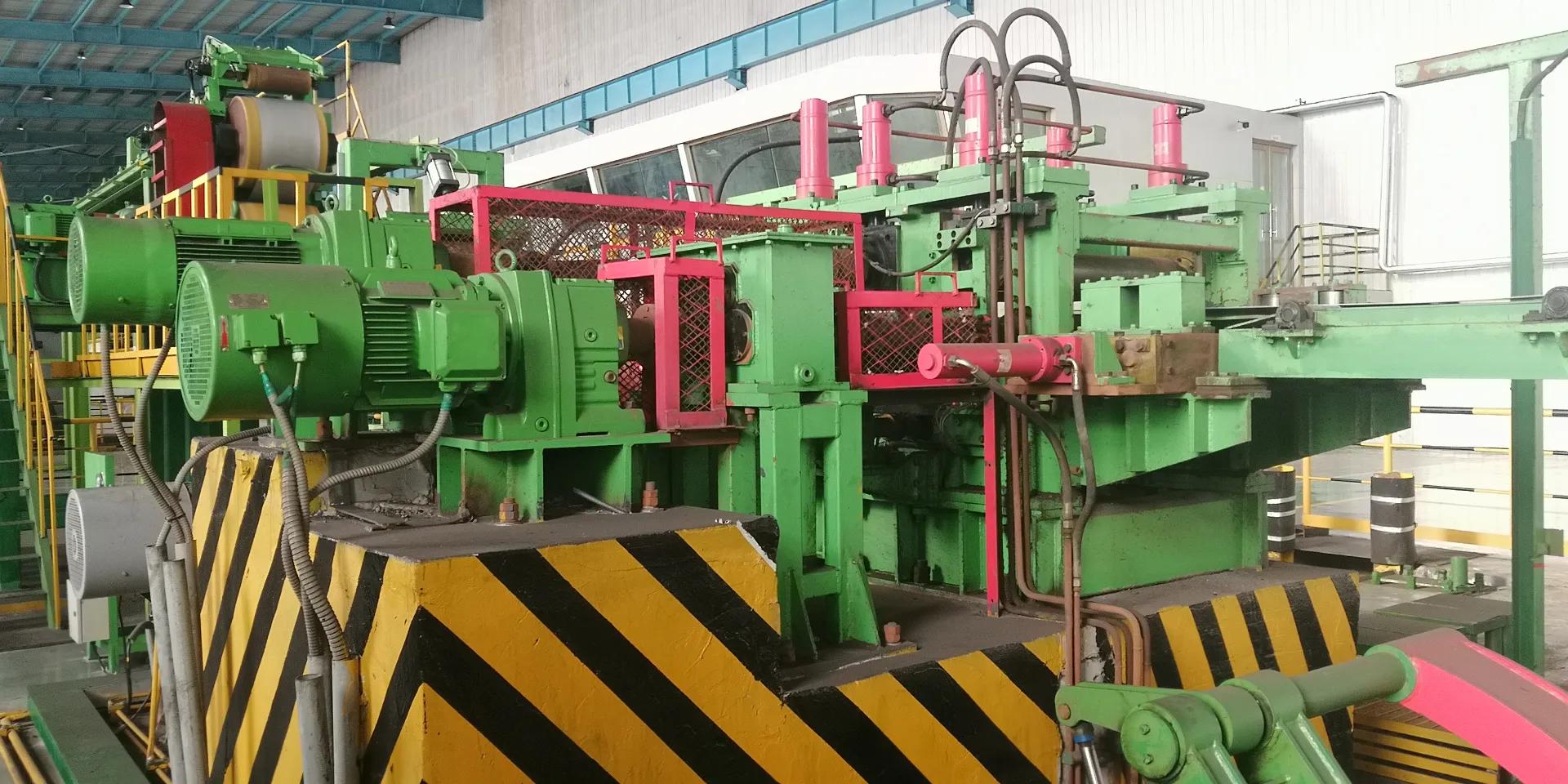
The journey of metal through a rolling mill is elaborate. Initially, metal stock is inscribed into the mill and subjected to high-pressure, high-temperature rolling—a systematic reduction in thickness producing elongated strips or sheets. This intricate process involves the manipulation of metal properties, employing principles of physics to enhance its structural integrity and finish.
Industrial rolling mills diversify into two main types hot rolling and cold rolling. Hot rolling occurs above metal recrystallization temperatures, producing thicker sheets often for construction applications. Cold rolling, performed at room temperature, yields finer surface finishes and greater dimensional accuracy. These distinct methods cater to various industry demands, demonstrating versatility.
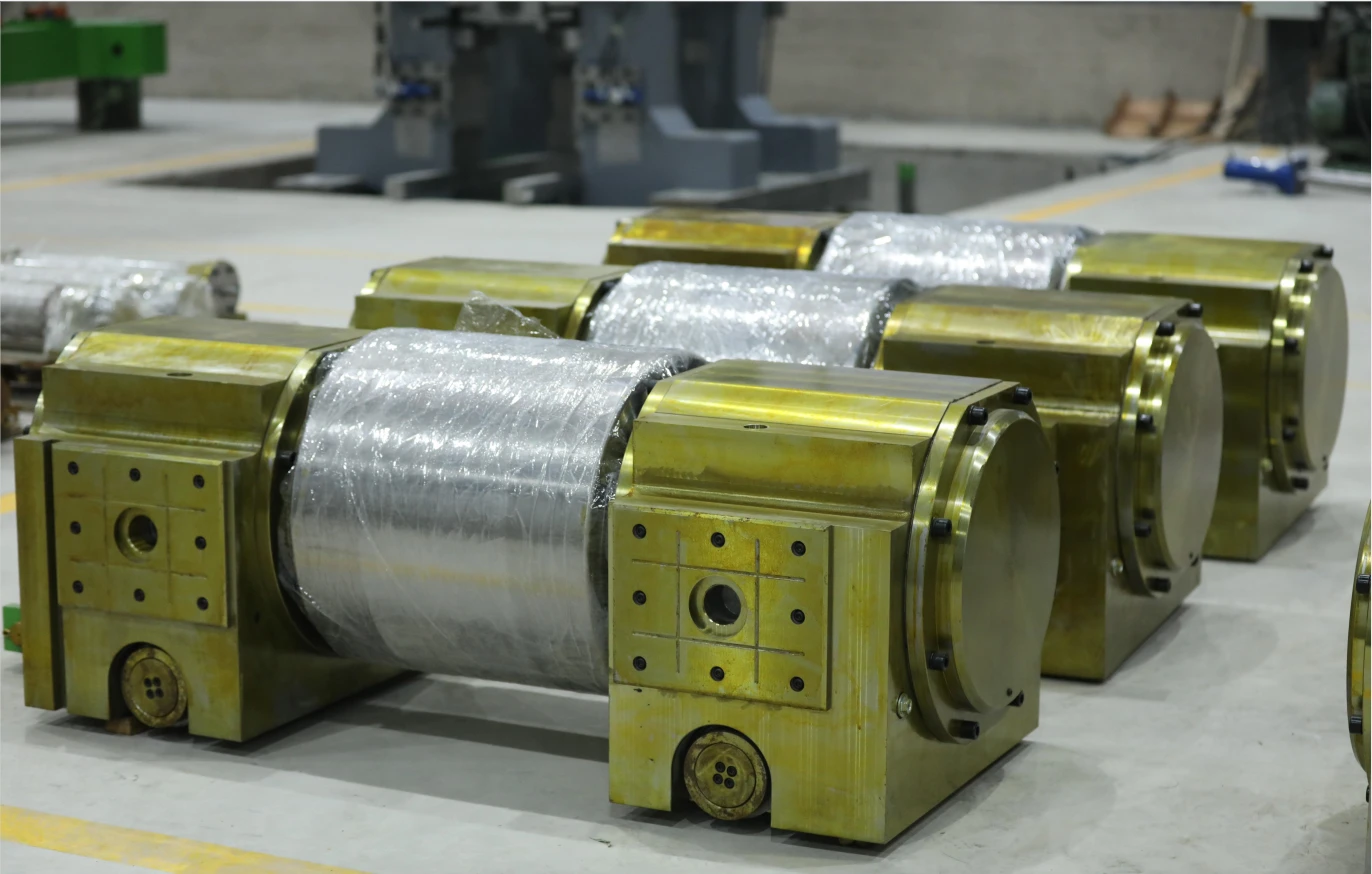
Advanced technology enhances the performance of modern rolling mills. Automation and digital control systems allow minute adjustments to roller alignment and pressure, ensuring uniform output quality. Real-time sensors offer precise measurements of force, temperature, and thickness, vital for quality control in high-stakes projects like aerospace or automotive manufacturing.
Experience plays a crucial role in optimizing rolling mill operations. Skilled operators, through years in the field, develop an intuition for machine adjustments under varying materials and environmental conditions. Their expertise ensures maximum output with minimal wastage, adhering to stringent quality standards. Understanding the interplay between equipment settings and final product characteristics distinguishes seasoned operators from novices.
industrial rolling mill
Manufacturers choosing rolling mills face critical decisions on type, capacity, and integration potential. Identifying a mill that aligns with their production scale and output requirements is paramount. Consulting with industry experts or suppliers who understand the nuances of machinery aids in acquiring the right equipment. Their authority in the field offers insights into future scalability options and maintenance considerations.
Trust in a rolling mill’s reliability stems from regular maintenance and adherence to safety protocols. Scheduled inspections, timely repairs, and employee training fortify a mill’s operational longevity, mitigating risks of unscheduled downtime. A trustworthy rolling mill not only maintains productivity but also assures stakeholders of compliance with safety and environmental regulations.
In summary, the strategic deployment of industrial rolling mills elevates manufacturing capabilities, integrating high efficiency with precision engineering. As manufacturing demands evolve, embracing technological advancements and expertise-driven practices ensures these machines remain indispensable. Investing in the right equipment backed by expert consultation assures not only optimized output but sustained operational excellence, setting benchmarks within the industry.
For businesses seeking to harness the prowess of industrial rolling mills, considering these facets—technology, experience, authority, and trustworthiness—ensures a competitive edge, securing a place at the forefront of modern manufacturing innovation.