In the industrial sector, especially in manufacturing processes involving metals, the skin-pass mill plays a vital role in achieving desired characteristics in steel products. Particularly in the galvanizing line, it is an indispensable tool for enhancing surface quality and mechanical properties. This article aims to delve into the intricacies of skin-pass rolling in galvanizing lines, illustrating its importance through real-world experiences and expert insights.
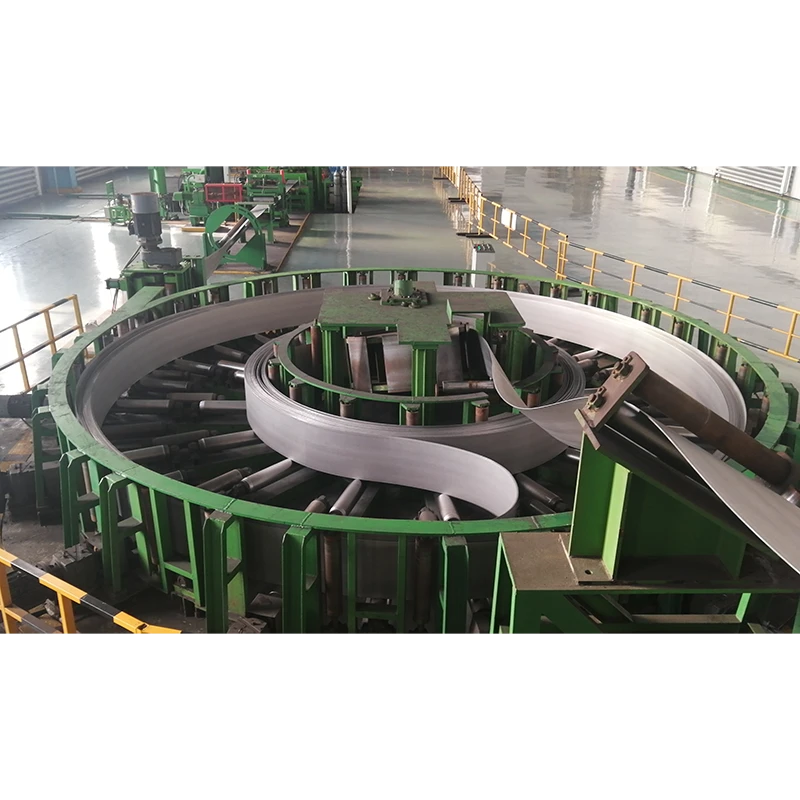
The skin-pass mill, often referred to as a temper mill, is a critical component in the production of high-quality galvanized steel. It is designed to achieve specific flatness, surface texture, and mechanical attributes that are not otherwise attainable through primary rolling processes. By applying a minimal reduction, typically ranging from 0.5% to 3%, the mill smooths out surface defects, enhancing the visual appeal and functional properties.
One of the paramount benefits of the skin-pass process is its ability to mitigate the formation of surface irregularities such as stretcher strains and catenary marks. These imperfections can undermine the structural integrity and aesthetic quality of the steel. Real-world applications reveal that the deployment of a skin-pass mill in a galvanizing line significantly reduces scrap rates by ensuring consistent product quality. In automotive and appliance sectors where surface appearance is paramount, this process proves invaluable.
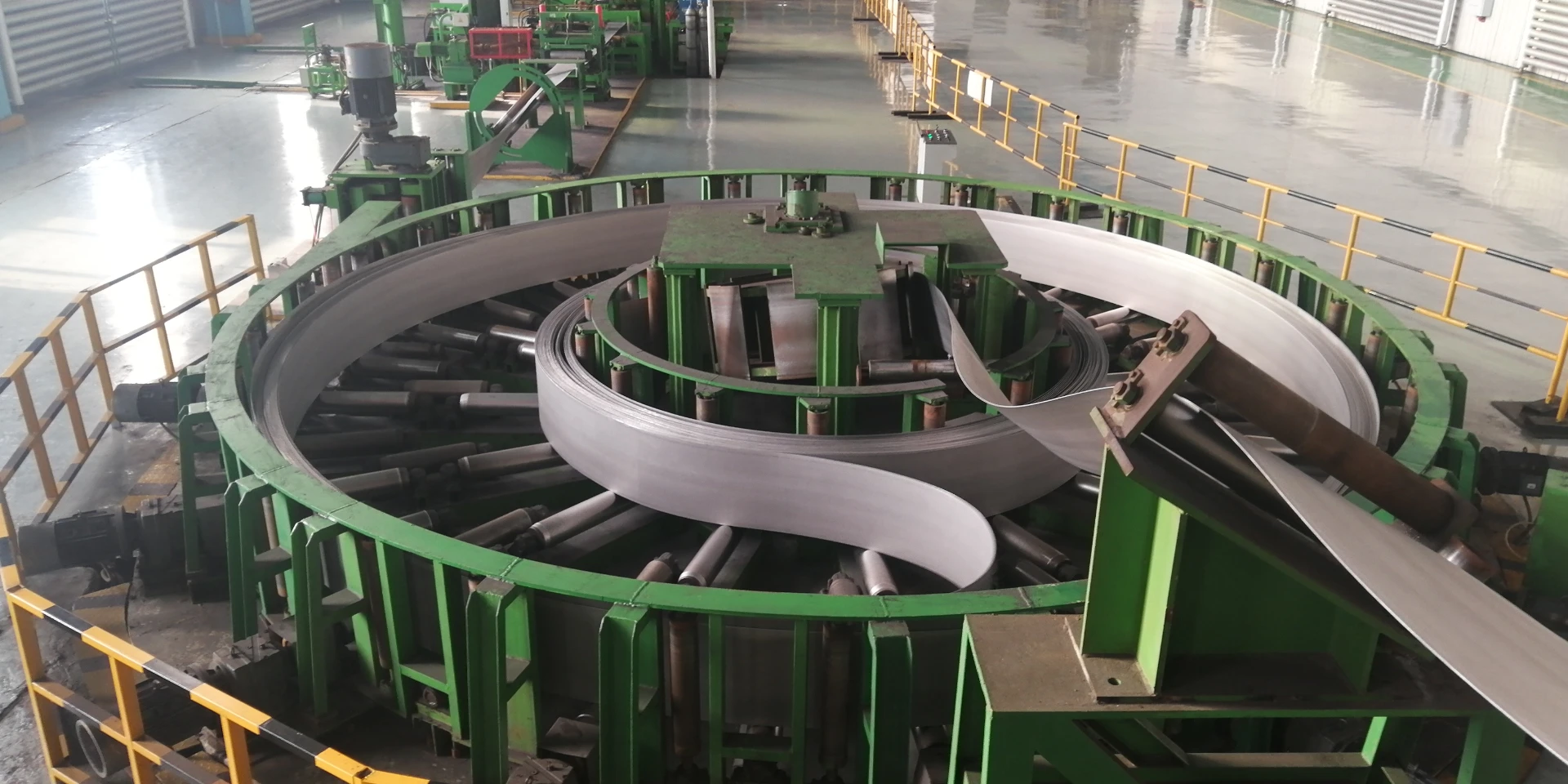
In terms of expertise, industry specialists underscore the importance of controlling variables such as rolling force, tension, and lubrication. Precision in these parameters ensures that the steel's mechanical properties, like tensile strength and elongation, are optimized without compromising the galvanic coating's adhesion or thickness. Engineers with years of experience in metallurgical processes attest to the fine balance required; too much reduction can lead to over-hardening, while too little can fail to achieve desired effects.
skinpass-walzwerk-verzinkungslinie
Moreover, the technology used in skin-pass mills has advanced significantly, encompassing innovations such as automatic gauge control and advanced surface inspection systems. These technologies enhance the mill's efficiency and output consistency, ensuring compliance with stringent industry standards. Leaders in steel manufacturing point out that adopting state-of-the-art control systems not only meets but often exceeds client expectations, thereby enhancing brand reputation and securing long-term partnerships.
From an authoritative standpoint, the relevance of skin-pass rolling in galvanizing lines is reflected in industry guidelines and specifications issued by professional bodies such as the American Society for Testing and Materials (ASTM) and the International Organization for Standardization (ISO). Compliance with these standards is not only a testament to quality but also to the mill's capability to operate within globally recognized frameworks of efficiency and sustainability.
Long-time clients and stakeholders in the metal processing industry often cite trustworthiness as a cornerstone of successful business relationships. They emphasize that consistency in product quality, enabled in part by reliable skin-pass operations, fosters trust between manufacturers and end-users. Testimonials from seasoned purchasers of galvanized steel products reflect an appreciation for the uniformity in quality achieved through skin-pass rolling—a factor that decisively influences their procurement decisions.
In conclusion, the skin-pass mill in a galvanizing line is not merely a piece of industrial equipment; it is a linchpin in the quest for high-caliber steel products. Through a combination of expert knowledge, advanced technologies, and adherence to global standards, the application of skin-pass rolling underscores a commitment to excellence in steel manufacturing. Its impact resonates across the supply chain, corroborated by endorsements from industry veterans and satisfaction from informed consumers. As manufacturing evolves, the role of the skin-pass mill continues to be integral, adapting to new challenges and driving forward the pursuit of metallurgical perfection.