Exploring the intricacies of tension control in winders offers a unique gateway into optimizing industrial processes that pivot on precision and quality. As a cornerstone of various production lines—ranging from textile manufacturing to paper and film industries—achieving the optimal tension in winding operations translates into increased operational efficiency, product quality, and reduced waste.
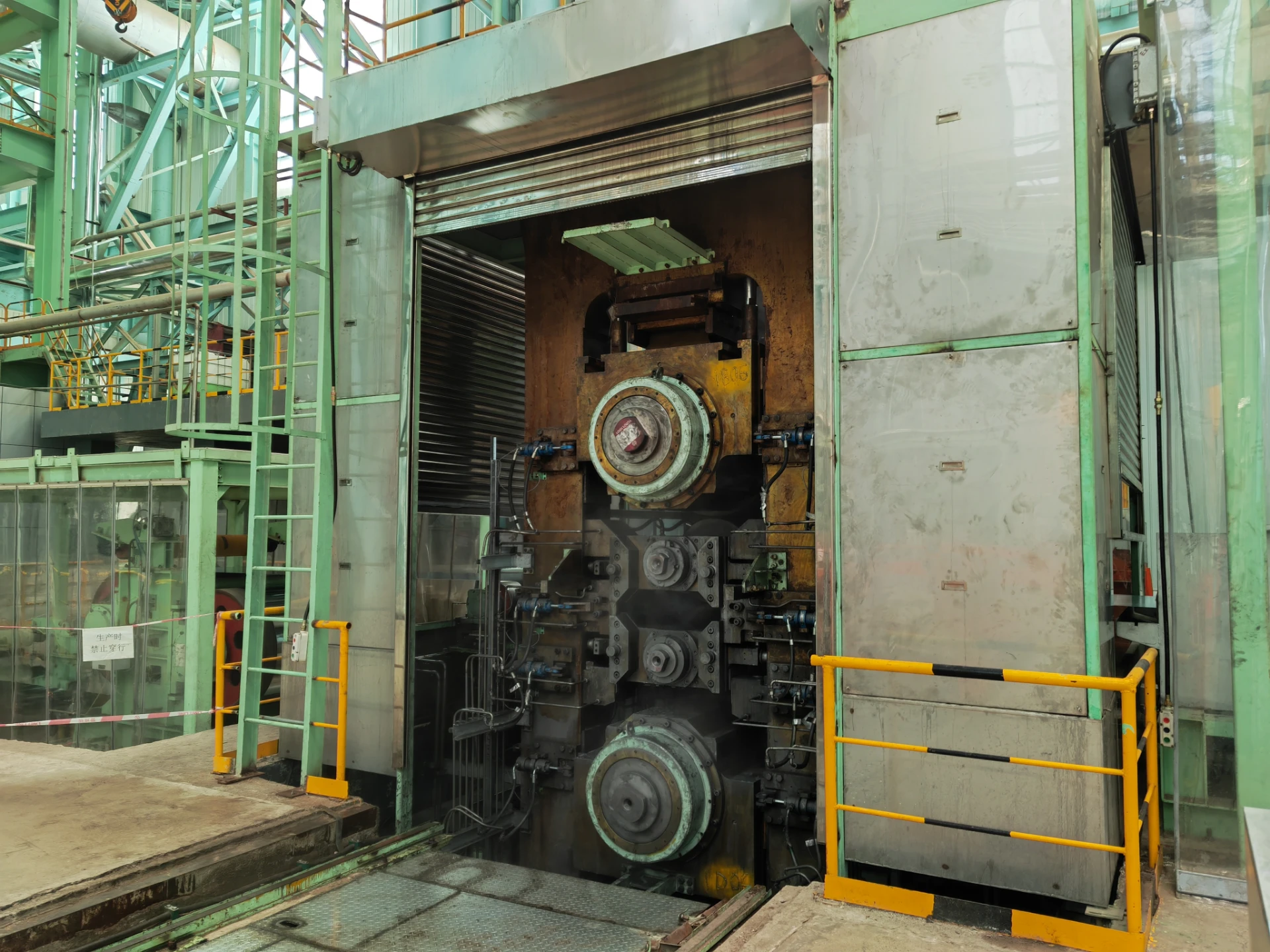
Understanding the Basics
In the realm of winding operations, tension control is pivotal. Tension refers to the force applied on a material being wound onto a spool or reel. Inadequate tension can lead to production anomalies such as wrinkles, stretch marks, or even breakage, while excessive tension poses the risk of structural deformation or material tearing. Optimal tension control ensures that material is uniformly and reliably wound, meeting the required specifications and standards.
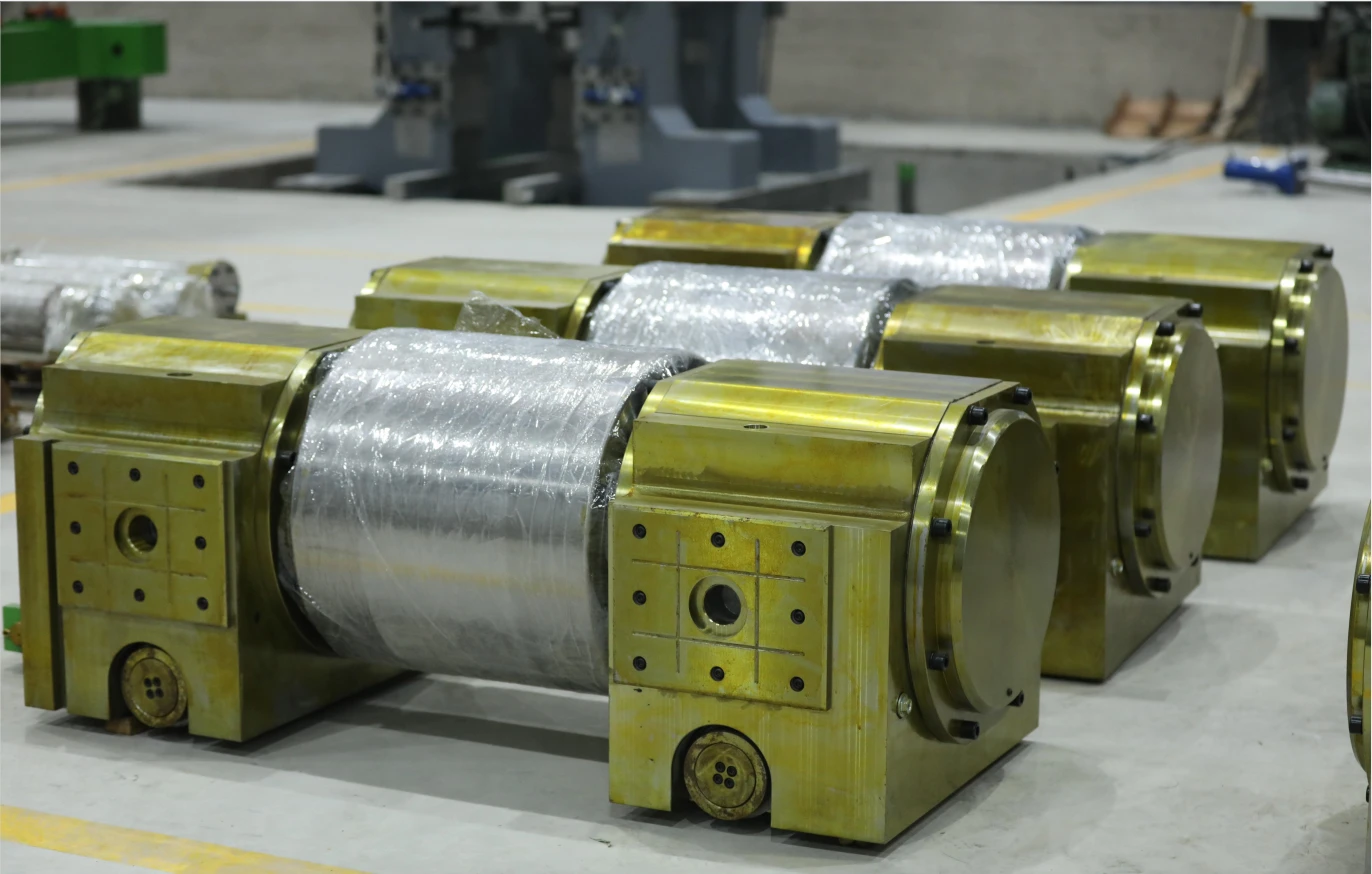
Advanced Techniques in Tension Control
Modern winders have transcended traditional methodologies by integrating advanced technologies that enhance tension control accuracy. These include
1. Dancer Roll Systems By adjusting the positioning of a dancer roller, these systems maintain consistent tension by compensating for any fluctuations. This method is particularly effective in applications involving delicate materials where precision is paramount.
2. Load Cells These devices directly measure the tension of the material being wound. By providing real-time data, load cells enable immediate adjustments to maintain desired tension levels, addressing inconsistencies promptly.
3. Closed-Loop Control Systems Utilizing feedback from tension sensors, these systems adjust motor torque dynamically, ensuring the tension remains constant, even with changes in roll diameter or line speed.
Integrating such technologies not only enhances quality control but also curtails downtime, thereby boosting productivity.
Expert Insights into Tension Control Challenges
Implementing efficient tension control systems requires deep technical knowledge and understanding of both machinery and material properties. Industry experts emphasize the importance of
winder tension control
- Material Characteristics Different materials respond uniquely to tension. For instance, elastic materials require different handling than rigid substrates.
Understanding these nuances is crucial.
- Environmental Factors Ambient conditions such as humidity and temperature can affect tension outcomes. Professionals need to account for these variables to achieve consistent results.
- Machine Calibration Regular maintenance and calibration of winding equipment are essential to ensuring that tension control systems function effectively. Neglect can lead to drift, undermining efficiency.
Industry leaders underline the significance of training operators to recognize tension-related issues swiftly and respond with corrective measures. Combining expert knowledge with cutting-edge technology maximizes the return on investment in winding systems.
Establishing Authority in the Sector
To truly establish authority in the field of tension control for winders, participating in collaborative research and advancements is pivotal. By contributing to industry standards and innovations, companies demonstrate their expertise and commitment to excellence. Sponsoring studies and sharing findings in relevant industrial forums can underscore a company's leadership position and build trust with clients.
Reliability Through Trust
In the industrial world, trust is a currency earned through consistent performance and quality assurance. Companies can build trust by
- Regularly updating clients with insights on how tension control optimizes their specific operations.
- Showcasing case studies that highlight past successes and future aspirations.
- Offering guarantees tied to performance metrics, underscoring confidence in their technology and processes.
The journey to achieving impeccable tension control in winders is one that blends technical acumen with cutting-edge technology. As industries continue to strive for operational excellence, the role of sophisticated tension control systems becomes even more integral. By leveraging expertise, dedication, and continuous learning, companies can not only meet but exceed industry expectations, securing a robust future in a competitive marketplace.