In the realm of industrial manufacturing,
precision and efficiency are paramount. One critical aspect that often determines the quality of final products is the control of winding tension. A deep dive into the intricacies of winding tension control reveals the significance of this process and offers insights based on real-world experience and expertise in the field.
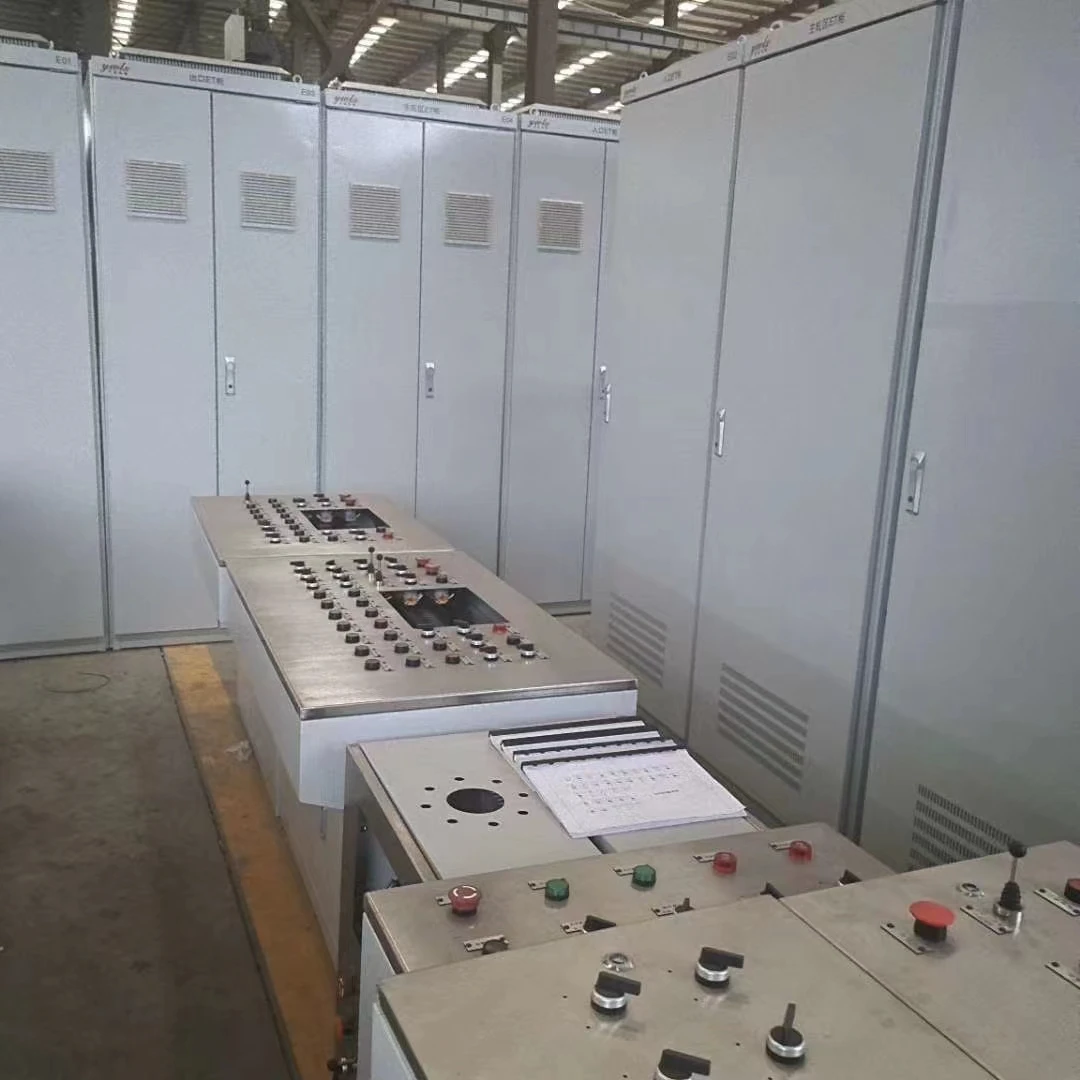
The journey towards mastering winding tension control begins with understanding its foundational role in manufacturing. Essentially, winding tension control refers to the regulation of the force or pressure applied to a material as it is wound onto a bobbin or core. This seemingly simple process is crucial across various industries, from textiles to electronics, where the integrity and uniformity of the wound material can directly impact the functionality and durability of the product.
Expertise in winding tension control is not merely about maintaining consistent pressure. It involves a sophisticated understanding of the materials in use, their physical properties, and how they interact with different levels of tension. For example, in the textile industry, the finesse of the fabric often relies on precise tension control to prevent stretching or distortion during the winding process. Similarly, in the manufacture of electric coils, ensuring the right tension means maintaining the optimal conductivity and performance of the wire used.
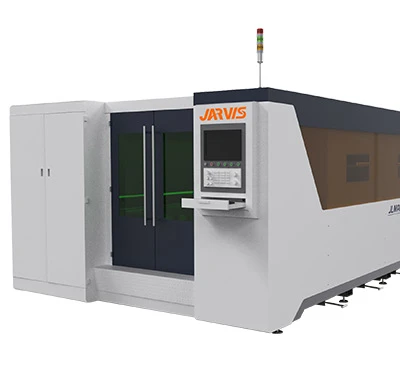
Authoritativeness in this domain is achieved through a comprehensive grasp of the technological advancements and machinery that facilitate optimal tension control. Modern machinery comes equipped with advanced sensors and feedback systems enabling real-time monitoring and adjustment of tension levels. These systems are predicated on algorithms that interpret material characteristics and external conditions, ensuring the perfect balance between tension and material integrity.
winding tension control
Real-world experience underscores the necessity of routine calibration and maintenance of winding equipment. The real-time data generated by these machines need to be analyzed to adjust operations appropriately, allowing manufacturers to prevent issues before they compromise product quality. Moreover, understanding the idiosyncrasies of each material and its behavior under various tension scenarios comes from hands-on experience and continuous learning.
Trustworthiness in executing winding tension control lies in the seamless integration of human oversight with advanced technology. Skilled operators equipped with both technological tools and experiential knowledge form the backbone of trustworthy tension control operations. Regular training programs ensure that operators stay abreast of the latest technological developments and methodologies for tension control.
Furthermore, collaboration with equipment manufacturers and material scientists enhances the depth of understanding necessary for handling new materials or innovative product designs. This collaborative approach guarantees that all stakeholders are aligned towards the common goal of maintaining superior quality control, thus reinforcing the trust clients place in the manufacturing process.
To encapsulate, the control of winding tension is an indispensable facet of manufacturing that harmonizes expertise, cutting-edge technology, and empirical knowledge. Learning from historical data while embracing technological advancements allows for the creation of products that meet high standards of quality and reliability. Therefore, mastering winding tension control is not merely about optimization; it's about pioneering excellence in manufacturing processes, thereby delivering products that stand the test of time.