Rolling mills play a crucial role in metalworking, transforming raw materials into finished products through deformation and rolling. Understanding the diverse types of rolling mills is essential for any industry professional. This knowledge not only ensures the selection of the most suitable equipment for a specific task but also enhances productivity, product quality, and energy efficiency.
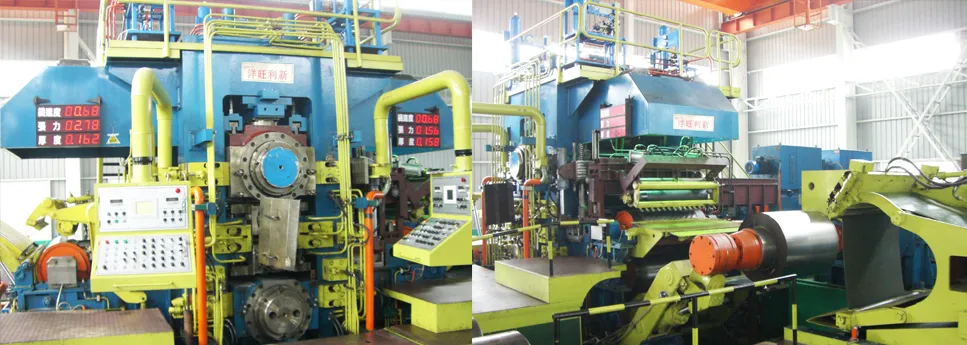
One of the most common types of rolling mills is the two-high rolling mill. This configuration features two opposing rolls and is primarily used for hot or cold rolling of metal sheets. Its simplicity makes it an appealing choice for projects that do not demand complex operations or tight tolerances. In many cases,
these mills are tandemly arranged for higher throughput.
More advanced is the four-high rolling mill, which introduces backup rolls that support the smaller working rolls, enabling the mill to achieve the precision necessary for thin materials. The backup rolls increase the rigidity of the working rolls, allowing for greater reduction and less deflection. This makes the four-high rolling mill ideal for producing foil, strip, and thin sheet products, where precision and finish quality are paramount.
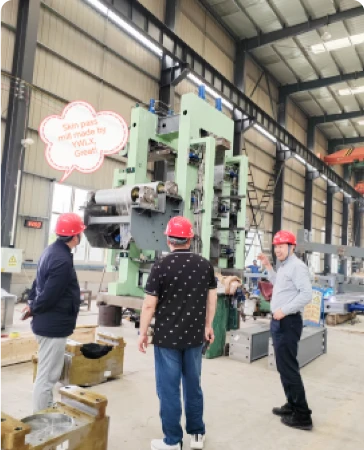
For tasks requiring even greater precision, a six-high rolling mill offers additional backup rolls, thereby minimizing the effects of roll bending. This mill type is highly adaptable and can handle a wide range of thicknesses and material types. It is especially useful in the manufacture of high-quality surface finishes and complex cross-sectional profiles, often found in advanced aerospace and automotive applications.
Cluster or Sendzimir mills represent further innovation, utilizing a combination of small-diameter working rolls supported by a cluster of smaller, backup rolls. This formation significantly reduces roll deflection, equipping these mills to handle exceptionally thin materials while maintaining surface integrity. Predominantly used for stainless steel and non-ferrous alloys, these mills meet the demands of industries that require ultra-thin, high-tolerance products.
The kind of light damage
Another noteworthy type is the planetary rolling mill, where each rolling station comprises a pair of large-diameter backup rolls that support a planetary array of smaller work rolls. The smaller rolls support extreme reductions in thickness per pass, making these mills ideal for processing brittle or difficult-to-deform materials. Their unique configuration aids in achieving substantial reductions while maintaining material properties, beneficial for specific applications like heavy-duty industrial components.
Continuous rolling mills offer an operational configuration for mass production, where multiple mills are laid out in succession. This system allows the material to pass through each mill without interruption, which is vital for high-volume production lines. Continuous mills are suited for processes that demand a steady and uniform output, such as tinplate or sheet metal production in consumer goods sectors.
The choice of rolling mill is often dictated by the material properties and end-product requirements. Material characteristics such as ductility, hardness, and temperature tolerance will influence whether a hot or cold rolling process is suitable. Simultaneously, the desired end product, whether it's a heavy plate for shipbuilding, a precision foil for electronic components, or a lightweight strip for packaging, will shape the mill's configuration and operational parameters.
In today's competitive manufacturing environment, leveraging the right type of rolling mill can be the key to achieving operational efficiency and product excellence. By staying informed about advances in rolling mill technology and understanding the specific use-cases for each mill type, industry professionals can ensure that they meet their production goals while maintaining high standards of quality and economy. The evolution and optimization of rolling processes continue to drive innovation across various sectors, reaffirming the rolling mill's pivotal role in modern industry.